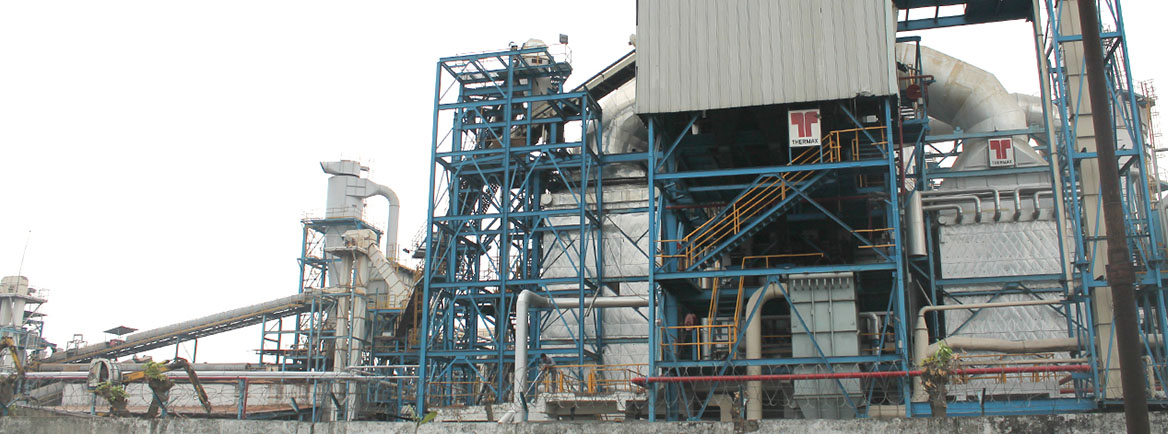
Thermax successfully commissions Asia’s largest energy plant for Greenply industries limited.
INTRODUCTION
Greenply Industries Limited is one of the leading interior infrastructure manufacturing companies in India and is primarily engaged in manufacturing, marketing, distribution of Plywood and Medium Density Fiber (MDF) Boards. The wood industry major has been associated with Thermax Limited for heating solutions for many years.In the year 2009, Thermax commissioned 50 MW Energy Plant in their Uttarakhand plant, which was the first engineered solution by Thermax supplying energy to multiple processes from a single energy efficient system. Reinforcing a decade-long association with Greenply,In March
2018 Thermax has successfully commissioned the second energy
plant of 97 MW. This plant is installed at Greenply’s state of the manufacturing facility for MDF board located at Chittoor,AP,India. It has an annual capacity of 3, 60,000 CBM and is the largest MDF plant in Asia and the fifth largest plant in the world. MDF is made by breaking down wood into fibers which are again combined with adhesives and the end product is formed into panels by applying heat and pressure.MDF boards are increasingly popular in many parts of the world for furnishing offices, schools and homes. Our esteemed customer is one of the market leader in India and have trusted Thermax for their expansion projects. Greenply being the Major plywood manufacturer in India understood the importance of replacing the traditional inefficient wood panels with wood efficient
MDF panels thereby ensuring sustainable economic development with
minimum burden on the environment and trusted Thermax with their
environment-friendly initiative.
Project details
Medium Density Fiber Boards are manufactured from agro plantation wood such as Eucalyptus, Subabul, Casurina etc. Wood logs are chipped and sent to a size separator (screen) where undersize wood chips are separated and reject is used as the fuel in the Energy plant. Then sized wood chips are sent to the Refiner where it is cooked with steam and converted into fibers. The produced fibers are mixed with appropriate resin and passed through the directly heated dryer. Flue gas from the energy plant is blended with ambient air so as to maintain a consistent temperature of hot gas required in the dryer. The dried fibers with appropriate moisture content then pass through a sifter, forming a line and feed to hot press (continuous press) to manufacture required thickness MDF board.
The heat required for the press is supplied in the form of hot thermal oil from the thermal oil heater at Energy Plant. MDF board from the press is further then sent to trimming and sanding system to get the boards of required size with smooth and even surface. The trim waste and sander dust generated in this process are used as fuel for Energy Plant.
3.6Mn capacity MDF Process as Chittoor plant had following heat requirements from Energy Plant. 50 MW for Hot gas at 350 deg C. 32 MW for Steam at 15 kg/cm2 (g) pressure and 15 MW for Thermal Oil at 290 deg C
Total thermal heat output of 97 MW with a solution on a turnkey with engineering, procurement, construction, and commissioning. Highest efficiency, lower emission, higher availability, automated control and safety systems were the prime criteria for selection of a supplier for Energy Plant system. Energy plant system should have flexibility in terms of fuel and load modulation/control.
The solution provided by Thermax
The challenge was to design largest capacity Energy Plant of 97 MW capacity and it should have fuel flexibility, highest efficiency, lower emission,higher uptime, automated control and safety systems for emergency situations.The critical components of Energy plant system such as combustor, pressure
parts,emission control equipment and control system were designed keeping in mind the above requirements. Some of the features are illustrated below
Combustor
Energy plant was required to be designed for multiple fuels like woodchips, Indonesian coal along with process waste chips and sander dust.Traveling grate as combustor was best- suited system and sander dust fired with the burner at a secondary level.The system had refractory line separate combustor without any heat absorption surface which made the system highly flexible. Flue gas generated in the combustor is controlled at 900 deg C and further distributed to three independent system viz. boiler, heater, and hot gas generator
Pressure Part
Heat recovery was entirely done with flue gas mass hence it required a high amount of heat transfer surface area. Membrane panel assembly in the radiation area reduces flue gas temperature before entering into the convection section thus increase availability of the system. A cross-flow configuration convection section helps to get an optimum area. An online soot cleaning system gives better uptime of the system.
Both boiler and thermal oil heater had independent induced draft fan control for steady control on load, higher turndown for the system.
Emission control device
A typically old Energy plant system had dust cyclone which has a limitation in terms of high power consumption of main induced draft fan, frequent cleaning because of choking and higher emission. Thermax had to offer A Electrostatic Precipitator as emission control to address all issues of the cyclone. Overall it was one of its kind and the innovative solution given by any energy plant supplier and was well appreciated by Greenply.
Safety features
Thermax’s Energy Plant offers high safety standard, and some of them are:
- Emergency stack to avoid over-pressurization of the furnace
- Thermal oil emergency cooler to safeguard the fluid
- Auto-vent valve for the boiler to a safe start and stop of the system.
Impact Created
Thermax Energy plant utilizes almost all wood waste generated from the process as the fuel thus reduces consumption of fresh wood making it environment-friendly. It assures the highest thermal efficiency of 94% which is a benchmark in the solid fuel-fired systems thus ensures the lowest operating cost.
While catering to varying load fluctuations it has to turn down ratio almost to the tune of 1:5. Independent control of each stream makes the system more flexible.
Our pollution control devise Electrostatic precipitator (ESP) gives lowest emission as compared to conventional systems.
The plant has the highest availability which makes it most economical compared to other competitors.
Thermax’s EP offers a completely automated system with highest safety standards with various emergency controls in thermal oil, steam and hot gas.
Thermax is committed to give the best solutions to our customers, time and again have proven the metal with cutting-edge technology solutions which are energy efficient and cost effective.